In the quest for ever-improving quality and performance, the industrial world has employed statistical quality control techniques with great success. Laboratories also have adopted some SQC techniques, mostly in response to external reporting requirements.
But so far, most laboratories are not using SPC for its most powerful benefit: using statistical techniques for continuous process improvement in order to improve analytical confidence and capability.
With today's pressure to meet increasingly rigorous performance standards, laboratories have a ripe opportunity—and an urgent need—to take advantage of these proven statistical techniques, moving beyond pro forma reporting and adapting them for improving analytical results. This shift in approach requires laboratory managers to understand that 1) there is an underlying process in generating analytical results, 2) this process can be managed, and 3) the process must evolve through a program of continuous improvement.
To effectively use SQC for process improvement, laboratories must not only maintain and demonstrate analytical method stability, but they also must maintain and demonstrate proficiency, which is the capability to produce analytical results within the expected limits of method performance.
First Stability, Then Capability
To achieve and demonstrate analytical method stability, modern laboratory QA programs rely on control charts. These charts tell us whether the analytical method is stable and whether accuracy is being maintained. (QA procedures dictate that in out-of-control conditions we reject any data coming from the analytical method until we re-establish a state of statistical control.)
With the method's stability assured, we can now move toward capability. However, control charts do not tell us if the method's precision is acceptable. Most proficiency testing relies on examining results from analyses of known materials. Proficiency testing programs usually do not focus on the underlying analytical process nor do they provide laboratory managers with the tools to maintain and monitor analytical method capability.
The best method of determining proficiency is to use a statistical technique called process capability analysis. Originally developed for industrial quality management, process capability statistically describes the ability of a process to produce within specification. This method fits well within the requirements of demonstrating and managing laboratory proficiency.
Process capability (Cp) is defined as (USL - LSL)/6s, the ratio between the tolerance (upper specification limit to lower specification limit) and the ±3s process spread. A second commonly used index, Cpk, incorporates a measure of how well the process is centered around the target value in addition to a measure of process variation. Therefore, Cpk provides an indicator of process bias as well as variation. This index is the one most commonly used in current manufacturing practice. By providing indicators of both method bias and variation, Cpk is a powerful statistical tool for measuring analytical performance.
Managing and demonstrating laboratory proficiency must involve standardized procedures with universally accepted statistical tools. Although the literature of the use of Cp and Cpk in laboratories is minimal, the methods are well developed and characterized with fifteen years of literature and operational experience in industrial settings. Laboratory managers can benefit from these well-developed industrial models and use them to employ an established SQC tool that accurately describes laboratory proficiency while providing a means to evaluate and improve laboratory performance.
The calculation of process capability requires specification limits so that observed performance can be compared to expected performance. Typically analytical methods do not have specification limits in the classic industrial sense. An available alternative for analytical methods is the observed method variation from AOAC and ASTM collaborative studies. Since these values represent the variation found among a pool of laboratories, they could be used as method "specifications" for process capability calculations. Likewise, values derived from round robins or regional pools could be used where appropriate, recognizing that they are not as rigorous a procedure. Such values serve as a useful first approximation as we begin to study and define this approach to lab proficiency.
Process Capability: An Illustration
To illustrate laboratory process capability, consider the analysis of a standard material with a nominal value of 10. The analyses in the pool yield an expected variation of ± 0.9. The first step determines process stability using a control chart. Next, plotting our laboratory's analyses produces the following histogram:
This analysis provides a great deal of information on analytical performance. When Cpk is greater than 1.0, we can expect that the delivered analysis is within acceptable limits more than 99.7 percent of the time. Note that Cpk is lower than Cp, reflecting the fact that our analysis exhibits a small negative bias.
Laboratory management must establish the criteria describing a capable process. Cp and Cpk provide the best quantitative measurements of method performance.
With this information, we can make informed decisions on managing the process. For example, is the risk of producing analytical results outside of limits acceptable? Do we need to invest in improving our analytical process?
An Evolving Practice
Process capability can be a powerful tool for managing laboratory operations and making improvements to meet increasing demands for accurate and precise results. In addition to providing a generally accepted metric of laboratory performance, process capability analysis will reinforce process management models in the laboratory. The result will be more effective laboratory management and improved analytical performance.
These benefits are well within reach of most laboratories, but what is needed is a movement to spur the evolution of laboratory management as a process in which SQC techniques are used for continuous improvement. As more and more labs successfully adopt and evolve SQC methods to meet their needs, and as the literature documents those successes, there is no doubt that we will experience the forward leaps in quality that our partners in industry have enjoyed on the plant floor.
Jeffery L. Cawley, Vice President, Northwest Analytics, Inc.
Scientific Computing & Instrumentation Magazine
Published with permission.
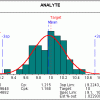